FISHFA BIOGENICS
Quality Management
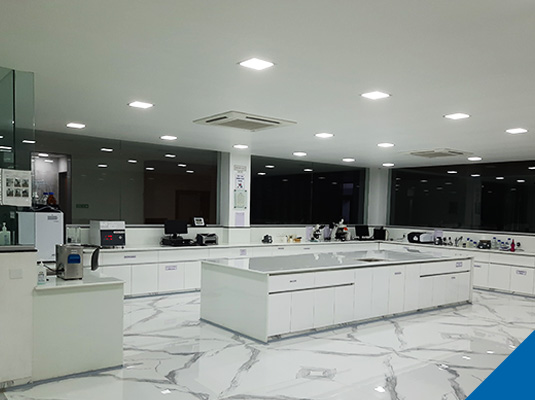
Quality
A deep-seated commitment to quality pervades all our activities. Our quality assurance processes ensure that we produce pure, safe and effective biological API that meet the highest quality standards that customer demand.
By keeping quality at the centre of everything we do, we are in the business to earned the trust of customers.
As a quality-focused biotech company, we train all our employees on quality assurance processes and adopt a zero-tolerance attitude to compliance violations. Our commitment to quality helps us manufacture biological API using innovative technologies and eco-safe protocols.
Harmonization of Compliance
Established global level documentation structure to ensure harmonized processes, methods and strategies throughout the organization. This concept enables planning, monitoring, and facilitating continuous improvement of product quality supporting regulatory compliance.
``Enlighten Learned`` Strategy
“Enlighten Learned” strategy is an integral part of our quality culture. The process includes assessment of gaps, their analysis, risk mitigation and taking necessary corrective actions and prevent similar occurrences.
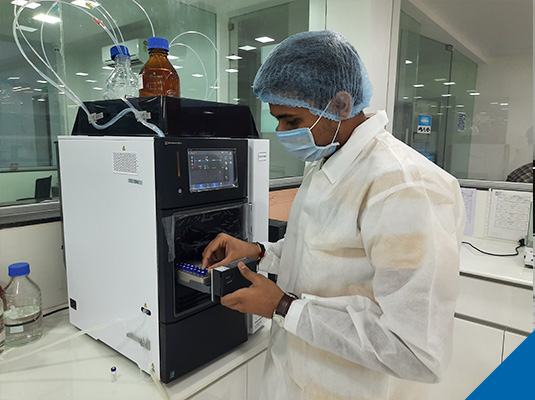
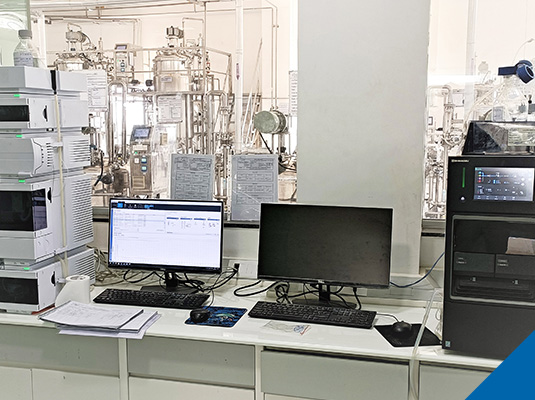
Quality Management Maturity (QMM)
We are achieving higher levels of QMM when they successfully integrate business and manufacturing operations with quality practices and technological advancements to optimize product quality, enhance supply chain resiliency, and drive continual improvement.
Quality by Design Principles (QbD) for Quality Improving
The basic concept of QbD is that “Quality cannot be tested into the product, but it should be built into it”. We are implementing a “21st Century Quality Initiative” across the organization including R&D, technical team and quality operations to perform quality, risk and knowledge management analysis.
High levels of QMM will lead to:
- Greater customer satisfaction
- Operational efficiencies –increase in productivity
- Higher revenues
Quality Data Management
We are investing in electronic applications, enabling the organization to establish harmonized processes through automation, develop site level metrics and indicators, and to put analysis and risk indication abilities to a new level of execution and control.
Assessment and Rubric
We are engaged to continually assess resources management, management review, business continuity, CAPA activities, change management, Manufacturing safety & operation, Demand forecasting, Process optimization, Understanding patient impact and Quality goals.